Positioning the Mechanical Codes and Standards (Example of the RCC-M)
- Philippe Malouines
- Nov 30, 2022
- 7 min read

Any nuclear project must comply with the nuclear regulation of the country where the equipment will be built and eventually operated. As safety rules vary from one country to another, technology-related choices for Structures, Systems and Components (SSC) are significantly country-dependent. To demonstrate the relevancy of a given customized design in more than one country is then costly and time-consuming; as such it is a true challenge.
Due to such customization to meet national requirements, the harmonization of Codes and Standards (C&S) continues to be unrealized in the international nuclear field. PWR [1][2] facilities provide an example of this lack of harmonization when referencing the mechanical codes for building the equipment of the nuclear island.
Historically, the codes were first developed by the industry, for the industry, to allow for design, manufacturing, operational monitoring and quality assurance (QA) methods that are robust in mechanical, material and scientific terms (calculation codes, etc.) and consistent with proven good industrial practices, while respecting the regulation(s) in force in the design-basis country. These codes, which reflect good practices validated by industrial experience, can then be recognized as compliant with regulatory and safety objectives, a priori in their entirety by the authorities, or only in part which requires additional justifications or adaptations to be accepted.
What is the need for Nuclear Codes and Standards?
Although the IAEA statute, established after the 2nd World War, makes it possible to issue recommendations applicable to all signatory countries for the peaceful use of nuclear technologies and applications, they remain non-binding recommendations. Each country is establishing its legislative system to operate nuclear facilities, primarily with a Nuclear Authority, which will enforce its national laws. The common approach is to request a Preliminary Safety Analysis Report (PSAR), satisfying the objectives of the Law. The content of the PSAR must demonstrate the achievement of safety objectives, in particular through technical choices.
An example is the choice of materials to ensure the break preclusion in a certain number of foreseeable situations, whether incidental, accidental or exceptional, and operating normally. In the United Kingdom, to have its reactor design approved by the Safety Authority (the ONR: Office of Nuclear Regulation), the technology vendor must go through a process called GDA (General Design Assessment). This is where the Nuclear Codes come into action; by meeting the requirements of the PSAR through a known/recognized code, the Safety Authority finds itself on a previously accepted area, placing the regulator in a more comfortable position with respect to the choices of the operator.
The ASME code (Sect. III div.1) is recognized by the Nuclear Regulation Commission (U.S. NRC) in the USA and facilitates the Owner-Operator/NRC relationship. In the United Kingdom, the Owner-Operator, EDF NNB GenCo[3], had to demonstrate that the RCC-M code satisfied the SAP (Safety Assessment Practices for Nuclear Facilities) requested by the ONR in the GDA process. The UK regulation does not impose any specific code, and the ONR was equally familiar with the ASME as RCC-M. The same approach was followed in Finland where it was necessary to demonstrate to STUK (Finnish Nuclear Authority) that the RCC-M satisfied the YVL (Finnish Safety Requirements).
In France, the Flamanville 3 EPR, the RJH[4] as well as ITER[5] projects have met with major regulatory changes while being developed (ESPN Order in 2005, INB Order in 2012, ...), and the RCC-M codes have been adapted during the course of the projects. In the case of materials, the technical qualification M140 of the RCC-M before 2005 was sufficient to support the demonstration approach of break preclusion, while the ESPN order, under the same term "technical qualification", required a complete questioning of this demonstration (essential parameters, analysis of risk related to material composition, ....). The UK regulatory SAP define High Integrity Components (HIC), which intersect with the technical qualifications of the RCC-M, but the SAP include additional demonstrations on the identification and possibility of in-situ measurement of defects.
Therefore it is crucial for the Owner-Operator, or his Vendor and design holder, to put forward C&S (Codes and Standards) solutions that are safe, proven and shared, as this will be well received and understood by the Authority.
Some countries do not impose limited C&S (e.g. United Kingdom), while other countries recognize several (Poland, South Africa, ...).
Since countries vary by the acceptance of which C&S that should apply, it follows that:
- the criteria and methods of the code must adapt to each regulation
- the guarantee of implementing these technical solutions is supported by the Quality Assurance approach, which will allow the Safety Authority to have a traceability that the operations announced a priori are documented, recorded, inspectable, as well when the project is under progress as retrospectively.
Here too, the C&S will provide a solid foundation for the designer, manufacturer, owner or operator vis-à-vis the Safety Authority:
- in addition to its technical solutions, the code can provide guarantees in terms of Quality Assurance: this is the case of ASME Sect IIII div 1, with the use of the NQA-1 standard, which is of the product-type Quality Assurance within a qualified organization ("ASME Stamp"),
- in addition to the code, requirements in terms of Quality Assurance can be made: this is the choice of RCC, which call for ISO 9001 as a basis, plus requirements from the IAEA quality management system recommendations. In 2022, the recent ISO 19443 standard was introduced, which complements the application of ISO 9001 with nuclear specifics, and in part is derived from the recommendations of the IAEA,
- the standards, whether NQA 1, ISO 9001, ISO 19443, in this field of quality systems, are often aligned and sometimes, although seldom, in contradiction, with mandatory national regulations. This therefore requires some "flexibility of adaptation" of the requirements of the codes. This problem appeared with ASME (with certification of the manufacturer “stamp”) in the United Kingdom, or in Finland as well as in China, both for ASME and RCC-M, with Chinese “HAF” regulation.
Standards, or norms if we place ourselves in Europe, serve to use the best of the industrial know-how recognized in the nuclear field. The RCC-M, for example, refers to more than 300 European or international standards, sometimes strictly French.
ASME is based on the American standards ASTM (materials), AWS (Welding), ASNT (Controls), and some rare EN or ISO. An American material (ASTM) A 106 for example, will become and called SA 106 if it is deemed usable on pressure equipment and mentioned in section II of the ASME.
Unfortunately, it will be more complex to use a material not mentioned by ASME. On the other hand, the long-term base material of an EPR is not defined in ASME Sect. II: it is up to the operator to complete the requisites of the base material of section II with its requirements of service life, aging and sensitivity to radiation, to obtain the ad-hoc "nuclear" material for 60 years of lifetime.
This difficulty is circumvented with the RCC-M (idem RCC-MR, RCC-Mx), which have developed materials dedicated to the reactor, vacuum torus or aluminum box, respectively.
The RCC-M has now freed itself from strict French standards, and the code opts for good European or International standardized practices. This trend is important to consider, because globalization brings the use of codes initially developed nationally, outside their original regulatory and industrial context. This was common with ASME and RCC-M, but it has developed since 2008, with Reactors installed in the United Arab Emirates, based on the Korean Code KEPIC[6] , but also for Russian reactors in Turkey and Finland, or Chinese reactors in Pakistan (Base Code RCC-M initially in the latter case). The globalization of markets is having an impact on the Supply Chain, and the Norms or Standards considered when localizing supplies are essential.
For example, in the RCC-M, with regard to non-destructive testing methods, only non-destructive testing by magnetic particle testing is based on the specific requirements of the code. The ultrasonic, dye penetrant and radiographic methods are primarily based on the EN or ISO methods.
Through these few examples, it is clear how the Technical Codes make it possible to meet the regulatory requirements. As regulatory requirements remain to this day country-specific, it would be wise to optimize the choice of code as soon as a project reaches its design maturity as such a choice has an impact on:
- the robustness of the demonstration vis-à-vis the safety authority,
- the design choices,
- the supply chain,
- and consequently, the cost of the project in a significant way.
To date when designs target is not a single country, but several regulations and the size of the projects shows huge differences (1700 MW vs 170 MW-SMR), unit or series, these C&S choices must be explicitly questioned, considering all their consequences.
European Vendors are familiar with the 3 approaches, in the case of PWRs, such approaches are:
- RCC-M, adapted to their domestic needs, e.g. French PWR (EDF) or Nuclear Propulsion and without change for export (Finland, China, UK, ...)
- ASME Sect. III div.1, without the qualification by stamp (ATMEA with MHI, Sweden, ... formerly French PWR in Belgium)
- ASME Sect. III div 1 with stamp (EPR USA (Studies), Steam Generators for the USA, Steam Generators for the Republic of South Africa, ...).
What is true for PWRs will remain true for other projects with an international vocation, whether high temperature reactors, fusion (Spherical Tokamak project for Energy Production in the United Kingdom), or molten salt SMRs.
Codes and Standards are complex, offering advantages to all parties, but with pitfalls when C&S harmonization is not yet apparent. Setting forth a Codes and Standards Plan at the beginning of significant projects can highlight the opportunities and navigate the inconsistencies.
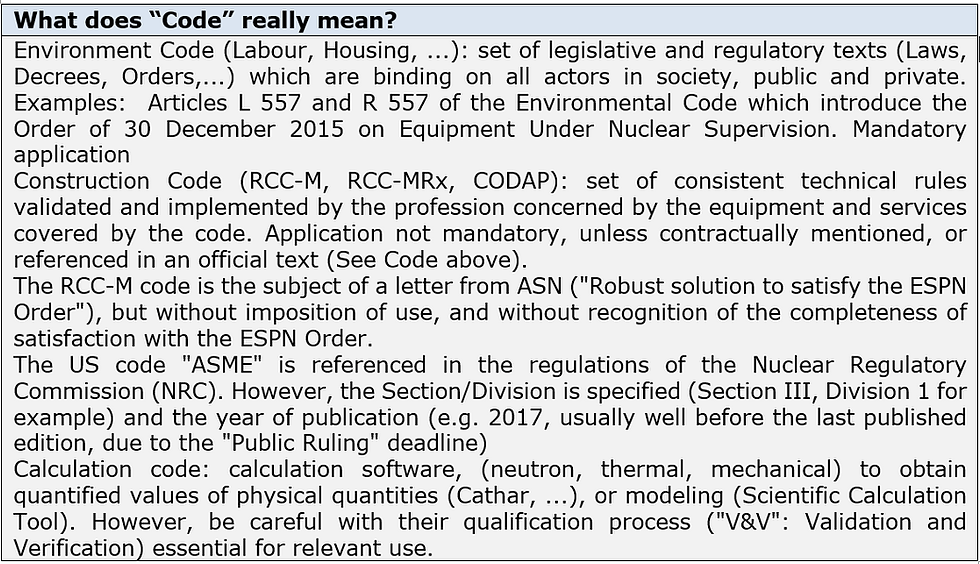
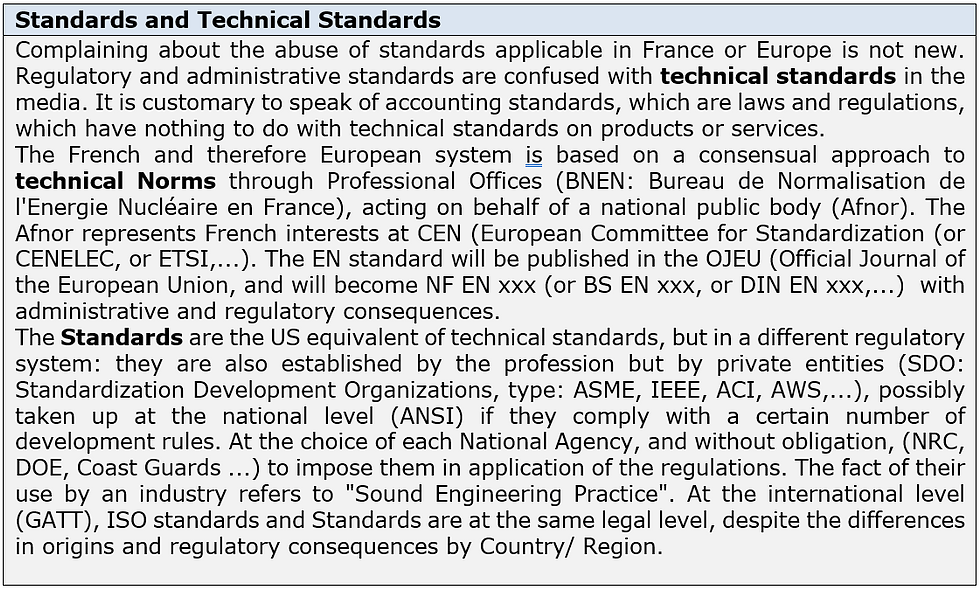
[1] RCC-M, ASME Sect. III division 1
[2] Pressurized Water Reactors
[3]Subsidiary to EDF Energy, Owner and future operator of EPRs in the United Kingdom
[4] The 'REACTEUR JULES HOROWITZ' (RJH) is a new research reactor dedicated to material and nuclear fuel testing. This reactor, which will be erected in the CEA Cadarache Nuclear Research Center.
[5] ITER is the fusion reactor located in Cadarache, FR
[6]Korea Electric Power Industry Code (KEPIC)
References
[1] J.M. Folz. “RAPPORT au Président Directeur Général d’EDF - La construction de l’EPR de Flamanville“ 2019 (in French)
[2] Serge Marguet. “La technologie des Réacteurs à Eau Pressurisée”, EDP Sciences, 2019 (in French)
[3] https://www.ecologie.gouv.fr/sites/default/files/2022.02.18_Audit_EPR2_RolandBerger_Synthese-1.pdf « La synthèse de l’audit sur les coûts du réacteur EPR2 commandé en 2019. « (in French)
Comments