The challenges of building modern nuclear power plants in the XXIst century.
- Jan Bartak, Noël Camarcat, NucAdvisor
- Nov 5, 2024
- 19 min read
Updated: Nov 6, 2024

1. Introduction
The schedule and cost overruns of recent nuclear new build projects with Generation III reactors are often compared with the experience of construction of the previous generation of reactors (Generation II), the “boom” period of nuclear power plant construction in many countries of the world, mostly concentrated in the years 1970-1990. The general impression is that we were entirely successful back then, and that the difficulties in recent nuclear new build projects with Gen III reactors can be solely attributed to the loss of competence, incomplete designs at the start of construction, poor organization and project management, inefficient supply chains.
There is no doubt that all the above played a role in the poor track record of the recent new build projects. But taking a closer look at the Gen II construction track record, the differences in design and in complexity between Gen II and Gen III, the evolution of regulatory requirements, the logistical and economic challenges, globalised supply chains, etc., it becomes obvious that Gen II and Gen III reactors are very different objects, designed, constructed and operated in very different technological, industrial, economic, financial, political and geopolitical environments. Many large Gen III reactors will have to be built in the coming decades, complemented by expected massive deployment of small modular reactors (SMR) and Generation IV advanced modular reactors (AMR).
Understanding this difference is essential to appreciate the challenges of new nuclear constructions and to take all the necessary measures and steps to make this endeavour successful. Success may not be sufficient on its own to mitigate climate change, but failure would mean putting the decarbonization of the energy and industrial infrastructure in jeopardy.
Construction of Generation II reactors - a contrasted track record
Cost and schedule reductions of the large-scale construction of Gen II reactors in the last quarter of the 20th century cannot be uniformly demonstrated for all countries that embarked on such programs fifty years ago. In a context where electricity utilities were in general integrated monopolies and electricity prices were regulated, the overall economy much less financialized than it is today, schedule and cost overruns were subject to much less scrutiny by the media, the general public and the politicians than they are today.
France adopted a standardized fleet approach for its large-scale Gen II PWR construction program launched after the 1973 oil crisis. Cost and schedule reductions were indeed observed. The data show that the strategy of standardisation of the French fleet with a vertically integrated industrial organisation (with the operator, EDF, having architect-engineer responsibility) allowed EDF to realise cost reductions between the first and last pair of each reactor series, even though quite marginal for the initial 900 MW series (Figure 1). Schedule reductions for sites where multiple units were built were also observed, even though it was not a general pattern. The average per GW construction schedule was 76 months for the 900 MW series (34 units), 68 months for the 1300 MW series (20 units) and 94 months for the 1450 MW series (4 units). For the last 4 units the “learning curve” was quite impressive: 110, 95, 93 and 76 months per GW from the first to the fourth unit, even though the FOAK (Chooz B-1) construction time had considerable delays related to I&C design and its licensing by the safety authority, as it was the first digital I&C system designed for a nuclear reactor.

Fig. 1: French nuclear program construction costs, 2012
The situation in the USA was quite different. The diversity of designs did not allow to benefit from the “learning by doing” schedule (and cost) gains that have been clearly demonstrated for the same reactor model built by the same firm in France and elsewhere [1]. The construction costs and schedules actually increased in the US as the number of reactors constructions grew, due to a multitude of causes: proliferation of safety regulations and codes & standards; owner/designer reaction to the rapid appearance of these regulations and codes & standards; rework caused by field interferences, constantly changing designs in response to new requirements, and inadequate engineering-to-construction lead times; extreme precision required in analyses, coupled with inflexible design and construction quality assurance requirements; management preoccupation with regulatory inspection, enforcement personnel site visits and regulatory reviews; and low worker morale, caused by all of the above [2]. The labour productivity dropped significantly after the TMI accident in 1978 and continued to decrease in the subsequent years.
Figure 2 indicates the average overnight cost of US plants with construction beginning in each year from 1967 to 1978. Vertical bars give the minimum and maximum construction cost in each year. The delays in construction times were the main driver of the cost creep.
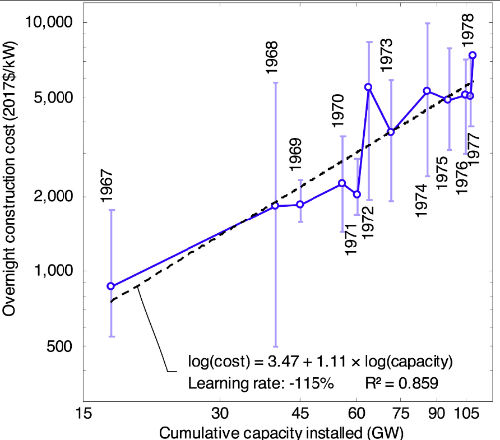
Fig. 2: US NPP construction costs with Gen II reactors [2]
3. Generation III reactors built in the Western world will cost more and will take longer to build compared to Gen II reactors
The common arguments explaining the significant cost and schedule overruns of practically all Gen III reactors new build projects go roughly as follows: we have stopped building new plants for two decades, experienced people had retired, the supply chain demobilized and lost qualifications and experience. Together with the initial Gen III optimism bias(1) and non-mature design at the start of construction, all this resulted in the schedule and cost overruns of Gen III new build projects. This narrative implies that launching again ambitious industrial programs and building a fleet of reactors will allow us to reproduce the “success” of Gen II construction. We have seen above that the “success” was quite relative and, as in the case of the US, non-existent.
There is no doubt that the presented causes contributed to the difficulties faced by the Gen III FOAK projects and that providing long-term visibility to the supply chain, placing orders for multiple power plants, optimizing the construction process, accumulating experience and learning from previous mistakes will all contribute to risk reduction and a better control of costs and schedules of the subsequent units.
Adopting the fleet approach is a necessary condition to keep costs and schedules of the subsequent units under control, but it does not tell the story about the fundamental differences not only between the Gen II and Gen III designs themselves, but also about a completely different economic, regulatory, financial, political and social environment compared to the last quarter of the 20th century.
The construction of Gen III nuclear reactors is significantly more complex than that of Gen II reactors due to multiple factors, some of them related to the reactors, their improved safety and their design (these are generally well known), some related to the external environment (regulatory, legal, economic). The most important of them are discussed in the subsequent sections.
(1) Initiated by Westinghouse and its marketing of the highly simplified and fully passive AP1000 reactor in the late 1990s, with the promise to build the reactor in 48 months. This threw down a challenge to the other vendors when competition was ramping during the pre-Fukushima nuclear “renaissance”. They had no other choice but to announce similarly unrealistic schedule and price targets.
3.1. Advanced safety features
Gen III reactors incorporate numerous advanced safety features that were not present in Gen II designs. These include first a much stronger civil work design for the reactor building. This is generally true after the 9/11 terrorist attempts on nuclear power plants in the US. It could be analysed in greater detail for the various GEN III models. Such reactors also include systematic multiple redundancy, physical separation and diversity of safety, emergency and safety-related cooling, electrical and control systems and equipment, passive safety systems, resulting in decreasing the core damage frequency by one or two orders of magnitude. These principles of redundancy, diversity, and physical separation are fundamental to the design philosophy of Gen III reactors. The core catcher and reinforced containment building capable of resisting the crash of a commercial airliner have become standard features for Gen III reactors. All these systems add complexity to the design, construction, erection, operation, maintenance, and decommissioning processes and drive up both the CAPEX and the OPEX. On the other hand, enhanced economic performance results from better fuel utilization and fuel economy, higher availability and longer design lifetime of systems, reduced volumes of produced radioactive waste etc.
An overview of the main differences related to enhanced safety is presented in Table 1. Assembling such a table is not an easy task. It can only be filled once the detailed design is completed thoroughly. But then important parameters have great economic value and are no longer available. Also, the correlations between these technical parameters and costs and delays are not straightforward, and often change between the conceptual design phase and the completion of the plant for start-up. In the context of this paper the objective is to underline the obvious additional requirements in terms of engineering effort, construction and erection time, and cost. Safety has a cost, something that is often forgotten when comparing construction performance of Gen II and Gen III reactors.
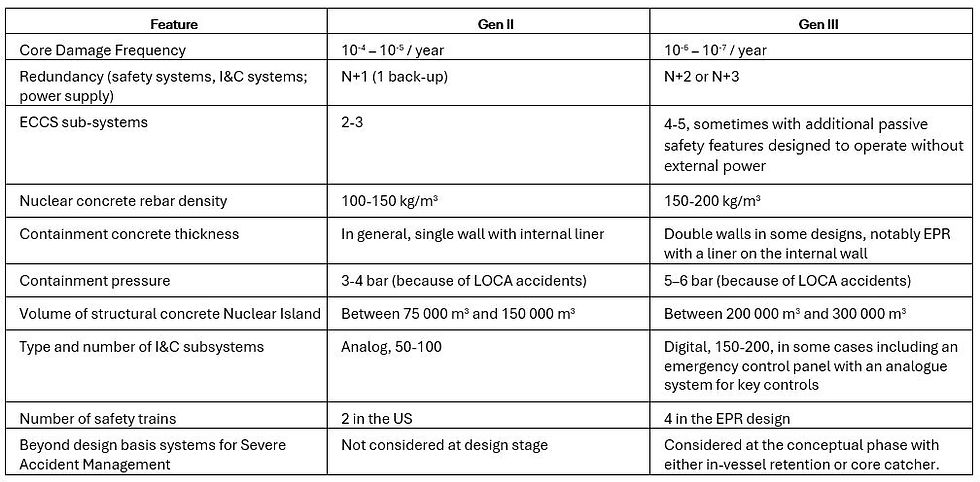
Table 1: Comparison of safety and economic features of Gen II and Gen III reactors
3.2. Regulatory requirements and public acceptance
Modern safety standards and regulatory requirements are much stricter and more comprehensive than those in place when Gen II reactors were built, the role of the “civil society” and the influence of public opinion, often grounded in emotions rather than in analysis, has increased dramatically. As an example of this evolution in relation to nuclear regulations, the following illustration taken from the French NPP construction history is revealing. More than half of the existing French nuclear reactors (i.e. over 30 units) started pouring nuclear island first concrete before the nuclear decree authorising the creation of the nuclear facility (DAC - Décret d’Autorisation de Création in French) was issued(2). The decree would be issued later, before the first divergence. But it was possible to start heavy nuclear construction before the decree issuance. Thus, the investor accepted a higher degree of risk with the benefit of an overall reduced construction schedule. The civil society was also willing to allow this higher degree of risk, and no nuclear plant divergence was blocked because of it. This is no longer possible today, and Flamanville 3 EPR first concrete was poured several months after the DAC was signed.
The evolution of nuclear regulations over time impacted the Gen II reactors in the US during their construction, as mentioned above, resulting often in significant delays due to re-design and modifications of already installed systems or components. The long design construction times of Gen III reactors were impacted by the increasingly rigorous regulations put in place after the TMI accident, after the Chernobyl accident(3) and more recently after the Fukushima accident, even though most Gen III designs were already largely “post-Fukushima – compliant”.
A short historical review of the evolution of the regulatory environment over the last 50 years is useful to understand the fundamental difference of the context under which Gen II and Gen III reactors were designed and built. The very concept of totally independent nuclear regulators establishing clear licensing guidelines was established progressively, during the last quarter of the 20th century, when Gen II reactors construction was already in full swing, based on often relatively simple safety principles produced jointly by scientists in research institutions and engineers from the vendor and operating organizations. The US Nuclear Regulatory Commission (NRC) was established in 1975 and a burst of new regulations occurred after the TMI accident in 1978.
The TMI accident focused attention on possible causes of accidents that the NRC and the nuclear industry had not considered extensively in the past. Their working assumption had been that the most likely cause of a loss-of-coolant accident was a break in a large pipe that fed coolant to the core. However, the destruction of the core at TMI had not resulted from a large pipe break but instead from a relatively minor mechanical failure that operator errors had drastically compounded. The NRC responded to TMI by re-examining the adequacy of its safety requirements and by imposing new regulations to correct deficiencies. It placed much greater emphasis on “human factors” in plant performance and developed more stringent requirements for operator training, testing, and licensing. It promoted the increased use of reactor simulators and the careful assessment of control rooms and instrumentation. The NRC devoted greater attention to other problems that had received limited consideration before the TMI accident, in particular the possible effects of small failures that could lead to major consequences, such as those that happened at TMI [3]. Significant research and code development programs were launched in the US and around the world to understand the ways in which “small breaks and transients” could threaten plant safety. The significant damage to the reactor core during the TMI accident triggered intensive research of severe and beyond design basis accidents resulting in core melting and possible loss of integrity of the reactor vessel. All these developments were integrated in the design of Gen III reactors and resulted in a burst of new regulations and safety requirements issued by the safety authorities.
Even though the US regulatory system was considered as a reference, different European countries developed their own, and sometimes rather different regulatory environments. In France the Gen II fleet was constructed based on a relatively simple and flexible regulatory context. This may be one of the reasons why average construction times of new reactors were six years in France and ten years in the US. The TMI accident produced technical innovation but did not have the same impact on the evolution of regulations as it had in the US. An important driver for a more structured regulatory environment in France was the willingness to export the French PWR technology. From the second half of the 1970s, in relation to the construction of the Koeberg NPP in South Africa, EDF and Framatome began to codify design and construction practices. This approach led to the adoption of a series of rules, the RCC (Design and Construction Rules), which were used as references for the design and construction of future French power plants, both nationally and abroad. Not being mandatory, the RCCs deal with all subjects related to the design and construction of nuclear reactors, even when they are not directly related to safety. Some of these RCCs, directly involving safety issues, were translated into fundamental safety rules (RFS) by the safety authority [4].
However, the trigger of a complete rethink and overhaul of the French nuclear regulatory system was the Chernobyl accident, coinciding with growing anti-nuclear movement and judicialization of the anti-nuclear movement with increasing numbers of court appeals to cancel or delay construction permits. Several major institutional changes in the regulation of nuclear risks were proposed and gradually implemented, in particular the creation of an institute bringing together expertise in safety and radiation protection (IRSN), independent of the CEA, and a Safety Authority independent of the ministries, all of which is governed by a law on nuclear safety. IRSN was created in 2002 and the law on Nuclear Transparency and Security (TSN) was finally voted in 2006, paving the way to the creation of the current, fully independent, Nuclear Safety Authority (ASN).
In 2008 ASN began a complete overhaul of the regulations by gradually replacing the old RFS with "guides" inserted into the traditional hierarchical regulatory structure based on the TSN law. This change was accelerated after the Fukushima accident in 2011progressively transforming the image of ASN to that of a « nuclear policeman ». This gradual change is accompanied by significant use of the instruments created by the TSN law – "regulatory requirements", then "decisions" – which are legally binding on operators. These instruments, which are made public (as well as the follow-up letters of ASN inspections, IRSN opinions and ASN guides), reveal a dynamic leading to a regime that is more transparent, open to the public, and at the same time more rigid in terms of regulations, since even satisfactory compliance can be challenged in court. One example for all, the ESPN (nuclear equipment under pressure) regulation changed several times between 2005 and 2018, every time increasing the design, qualification, fabrication, testing and control requirements imposed on the equipment to obtain regulatory acceptance Details about the difficulties induced by the changing ESPN regulations are detailed in the Folz Report [7]
A similar dynamic is observed in other European countries. After the Chernobyl accident, there is a growing awareness that environmental threats transcend national borders accompanied by a gradual desire to standardise regulation at the international and European levels, in particular through regulatory instruments such as the “Safety Reference Levels” developed by the Western European Nuclear Regulators Association (WENRA), an association of nuclear safety authorities in European countries, created in 1999. However, these standardization efforts were not efficient for some first Gen III designs in Europe. It is often said that EPR Flamanville judged sufficiently safe in France required 7000 modifications, some of them with major impacts on the Nuclear Island buildings to be licensed at Hinkley Point C in the United Kingdom.
For the European countries of the of the ex-Soviet bloc, their membership in the EU at the outset of the 21st century was conditioned by shutting down USSR-designed Gen II reactors that were considered non-compliant with western safety standards (RBMK in Lithuania and the VVER-440 V-230 type PWRs in Slovakia and Bulgaria) and improving the safety of the other ones. This was specifically related to the issue of the presence of reactor containment building as the third safety barrier, non-existent on the RBMK and VVER-440 reactor designs.
Apart from the nuclear regulator issuing the nuclear licenses, multiple other regulatory bodies and institutions at the national, regional and local level are involved. The environmental legislation and the depth of environmental impact analysis, the depth and detail of seismic, geological and geophysical studies cannot be compared with the requirements that existed at the time of Gen II construction. The regulations grew in numbers but also in complexity. Ensuring compliance requires often long periods of time and contributes significantly to the overall costs.
Finally, the society has changed. Public acceptance, transparent two-way communication and scrutiny from the public, NGOs, diverse lobby groups defending a variety of interests and the media has become a norm in western democracies, requiring considerable efforts and resources from the plant owner, the suppliers and all stakeholders involved.
(2) Dates of issuance of the nuclear decree and of the first divergence are available on the ASN website. For the Tricastin Unit 1 the time lapse between the decree and first divergence was 42 months. Since the construction of Tricastin 1 took 68 months, first concrete of the nuclear island happened 68-42 = 26 months before the nuclear decree.
(3) In particular, those 2 severe accidents gave rise to the Generation III doctrine: Core melt has to be taken into account at the conceptual design phase of Gen III reactors, since it can happen with a much higher frequency than previously thought, i.e. before 1979.
3.3. Technological innovations and design differences. The challenge of perfection in all nuclear tasks.
Gen III reactors utilize more sophisticated and technologically advanced components and systems compared to their predecessors. This includes improved fuel technology, advanced digital instrumentation and control systems, and more efficient and durable materials. Constructing and erecting these advanced systems is more technically challenging and resource intensive. The design differences typically involve larger and more complex containment structures, enhanced cooling systems, and integrated complex safety systems that require more intricate planning and execution during construction. Even though the capacity of Gen III units is typically larger than the capacity of Gen II units, and despite technical innovations (improved materials, increased efficiency of equipment like turbines, motors, pumps etc.), specific material consumption (per unit capacity) has not decreased. Structures designed for higher safety, like the containment and the core catcher add considerable amounts of rebar steel and concrete compared to Gen II. The containment structure must withstand both significant external shocks (aircraft crash) and higher internal pressures (5-6 bar), resulting in higher rebar densities. As a result, the specific amount of concrete (per MWe installed) of the EPR reactor is almost twice as high as of the Gen II PWR and the amount of steel is higher by ~25% [5,6].
The classification of systems and components and the much more stringent requirements on the safety class equipment increase not only the direct costs of such equipment but even more so the indirect costs related to their engineering, qualification, erection, construction supervision to ensure compliance with standards, and testing.
A common saying is that each technical gesture performed on an NPP project must be perfect at the first try. And industry performs of the order of tens of thousands of these gestures each day on such projects. Nuclear quality must be perfect, down to the order to 10-⁴ (one mistake each ten thousand tasks). Ordinary human life does not go below a few 10-³.
3.4. Project Management Complexity.
The project management aspect of building Gen III reactors is more complex for the reasons presented above (large plant capacity, complexity of design, stringent regulatory requirements), but also due to the involvement of multiple stakeholders, including regulatory bodies, technology providers with several tiers of sub-suppliers in often globalized supply chains, and construction firms. The project financiers, local communities, media scrutiny and NGOs require permanent attention of the project management, requiring larger management teams. These stakeholder engagement and management issues were virtually absent during the construction of the Gen II reactors. Gen III projects require substantial investments and longer construction timeframes, more sophisticated logistical planning to manage the procurement, transport, and installation of advanced components. The combined impact of more stringent regulatory requirements, design complexity, increased indirect tasks and activities and hence indirect costs, lack of project management efficiency, poor coordination of multiple trades working in parallel at the construction site etc., but also loss of experience (learning by doing), resulted in an overall decrease in labour productivity measured as the speed of material deployment (concrete, steel, bulk materials and equipment etc.), as illustrated for the US in Figure 3 [2]. The sharp drop in 1978 is the consequence of the TMI accident, but even after that labour productivity continued to decrease and the two sole Gen III projects (Vogtle 3, 4 and V.C. Summer) display lower material throughput than the last Gen II constructions.

Fig. 3 US nuclear industry material deployment ratio compared with 1976 [2]
In summary, the construction of Gen III nuclear reactors is significantly more complex than that of Gen II reactors due to the incorporation of advanced safety features, stricter regulatory requirements, technological innovations, design differences, the need to manage more sophisticated project logistics, and the economic challenges involved.
4. Way forward
First, it is important to acknowledge that nuclear new build projects are among the most complex and challenging construction endeavours ever undertaken. Harnessing the extremely dense source of energy with a level of safety and reliability exceeding the standards common to other industries requires a unique combination of a broad range of skills, highest quality workmanship, specialized materials, compliance with the most stringent standards.
The necessity to double electricity generation in the next 25 years to decarbonize the economy and produce hydrogen for industrial processes that cannot be electrified will require huge amounts of reliable nuclear generation, paving the way to serial construction of large nuclear fleets. However, the size and complexity of such projects requires us to think such serial construction at the scale of continents or very large countries like China or the USA. China may serve as an example in this respect. Having developed the impressive modern solar PV industry and its supply chain, China has progressively developed the scientific, engineering, industrial and organizational infrastructure allowing serial construction on nuclear power plants within 6-7 years with a progressive decline in construction times towards 5 years as the experience accumulates (Figure 4). The first Gen III reactors of foreign design built in China – four AP1000 (Sanmen and Haiyang) and two EPR (Taishan) units - had construction times closer to 9 years, the construction times of the first four plants with the Hualong One reactor – the domestic Gen III design – remained in the 6-7 years’ timeframe. This can be explained by the accumulated experience and uninterrupted construction process, but also by unfettered support from the government. Centralized decision-making allows for coordinated and streamlined processes. The government provides substantial financial support, including funding for research and development, subsidies, and favourable financing terms for nuclear projects. The construction process is highly standardized, enhancing efficiency, reducing costs, and shortening construction timelines. Standardization also facilitates easier maintenance and operational training.
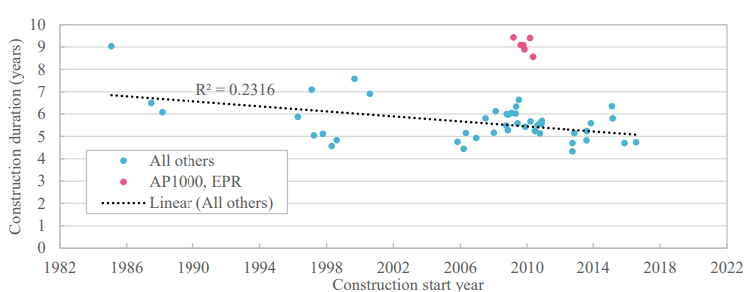
Fig. 4: Construction durations for nuclear plants in China [6]
Due to multiple regulatory, environmental and legal reasons, labour laws and regulations etc., but also the difficulties to roll-out serial construction at the same scale as in China, it is unlikely that similar construction times can be achieved in Western countries in the short term. The complexity of the Gen III designs and the highly complex licensing and permitting processes and their underlying legislation require deeper, diverse and more specialized supply chains and complex organization and logistics.
The United States are taking quite spectacular steps to create the necessary conditions for accelerated development of nuclear energy to reach their decarbonization goals. Following the COP28 declaration of 24 countries to triple nuclear generation by 2050, the US Energy Department (DOE) is taking concrete steps to triple US nuclear capacity by 2050, adding 200 GW to meet net zero emissions goals – a combination of large Gen III reactors in combination with a growing fleet of SMRs and Gen IV advanced reactors.
In June 2024, the US Congress passed an important ADVANCE Act, representing a turning point in allowing fast-track development of nuclear energy in the US. A few key elements of the Act are sufficient to appreciate the unprecedented nature of this policy shift:
U.S. Nuclear Regulatory Commission’s (NRC) mission statement has been updated to include conducting licensing in an efficient matter and in a way that doesn’t limit the benefits of civilian use of nuclear energy and radioactive materials - providing reasonable assurance of adequate protection of public health and safety, promoting common defence and security, and protecting the environment.
NRC to streamline licensing reviews:
Expedite reviews of combined license applications (COLs) - NRC to issue decision within 25 months of docketing;
Within 3 years, implement a risk-informed and performance-based process to license micro reactors;
Issue a report to Congress on streamlining environmental reviews, including use of categorical exclusions and generic environmental impact statements.
Addressing licensing fees for advanced reactors:
NRC to limit fees to be charged to advance reactor applicants;
Make available advanced reactor prizes to cover licensing costs for the first licensees to secure operating licenses (OLs) or COLs.
Investment into the US nuclear industry
If the EU wants to keep pace with the development of nuclear energy in the US, it would be well advised to take inspiration from these initiatives. Unfortunately, nuclear ambition is not yet shared by all EU Member States, to the detriment of EU’s energy sovereignty and independence. In May 2023, 16 European countries participating in the “nuclear alliance” agreed to prepare a roadmap to develop an integrated European nuclear industry reaching 150 GW of nuclear power capacity in the EU’s electricity mix by 2050.
Extending the lifetime of the existing fleet (assuming that all the reactors of the existing fleet can be extended, which is probably an optimistic assumption) will provide some 35GW. This means that 115 GW of new nuclear capacity will have to be built in 25 years. Nucleareurope, the EU nuclear industry association expects that this capacity will be composed of 56 GW of gigawatt-scale (Gen III) reactors, 50 GW of SMRs and 11 GW of advanced (Gen IV) reactors [8]. In other words, about 2 large reactors will need to be put in service every year. The SMRs will reach the market after 2030, implying 2.5 GW installed annually between 2030 and 2050. With an average size of SMRs of 300 MW, this amounts to 8 SMRs every year. The advanced reactors will probably reach the market only in the decade 2040-2050. No EU country can implement such a program alone. To preserve EU’s emergency independence, such a program requires a pan-European supply chain and close cooperation between Member States willing to develop nuclear energy, irrespective of the origin of the technology deployed. In the fierce global competitions, Europe should actively support the development of homegrown designs to compete on the global markets. Achieving such ambitious targets is going to require significant efforts from all stakeholders: industry, policymakers, financial institutions etc.
The industry will have to invest massively in the workforce throughout the value chain and develop a European supply chain. Increasing project delivery certainty and clearly articulated government and EU support through the recognition of nuclear energy as a major contributor to EU’s energy goals in terms of decarbonisation, affordability and security of supply will be essential to attract financing institutions and reduce the cost of capital. This means that the principle of technology neutrality must be respected across the EU policies related to electricity, heat, hydrogen, the Net Zero Industry Act and the different EU financing mechanisms.
We hope that the new European Parliament and Commission will make the development of nuclear energy the cornerstone of their economic, industrial and environmental agenda, based on the understanding that a strong EU cannot be built without large quantities of low-carbon, affordable and reliable energy with limited dependence on external resources and that in this endeavour nuclear energy is an irreplaceable contributor to achieving for EU’s sovereignty, industrialization and decarbonization.
References
[1] L.E. Rangel, M. Berthélemy: Nuclear reactors’ construction costs: the role of lead-time standardization and technological progress, Int’l WPNE Workshop “Project and Logistics Management in Nuclear New Build”, Paris, 2014.
[2] P. Eash-Gates et al.: Sources of Cost Overrun in Nuclear Power Plant Construction Call for a New Approach to Engineering Design, Joule, V. 4, Issue 11, 2020.
[3] J.S Walker, T.R. Wellock: A Short History of Nuclear Regulation, 1946–2009; US NRC, 2010
[4] M. Mangeon, F. Pallez: Réguler les risques nucléaires par la souplesse : genèse d’une singularité française (1960-1985) ; Annales des Mines – Gérer et comprendre, 2017/4, N°130, pp. 76-87 [5] Per F. Peterson, H. Zhao, and R. Petroski: Metal and Concrete Inputs For Several Nuclear Power Plants, University of California, Berkeley, Report UCBTH-05-001, 2005conference on the stress corrosion cracking phenomena observed on the French nuclear fleet, 29 March 2023
[6] W.R. Stewart: Capital cost evaluation of advanced reactor designs under uncertainty and risk; MIT, 2022
[7] J. M. Folz « Rapport au Président Directeur Général d’EDF. La construction de l’EPR de Flamanville ». On ESPN regulation, see pages 22-25.
Comments